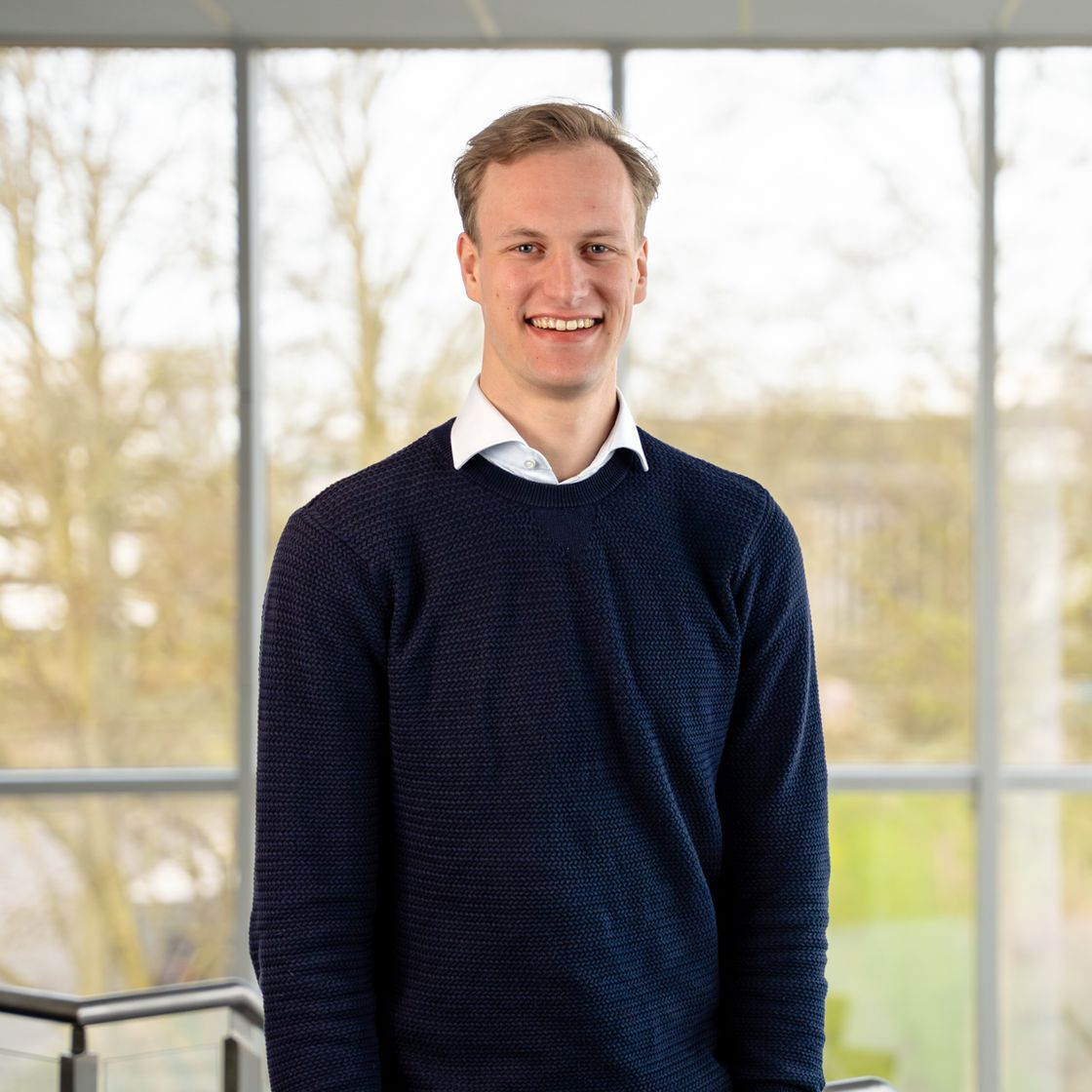
highlights
• various concepts generated
• closed-loop argon cryogen loop
• temperature control at 87 Kelvin
choosing the best option.
Due to various reasons, the milling process required (liquid) argon to be used as a cooling fluid. Six different concepts were created to generate the required cooling power at the location of the actual milling. These concepts ranged from a liquid-cryogen-loop using an external cryostat and liquid nitrogen liquefier as a precooling stage to an open-loop Linde-Hampson cycle combined with a Stirling liquefier cycle. A concept choice trade-off was than made based on cost, complexity and required cryogenic infrastructure.
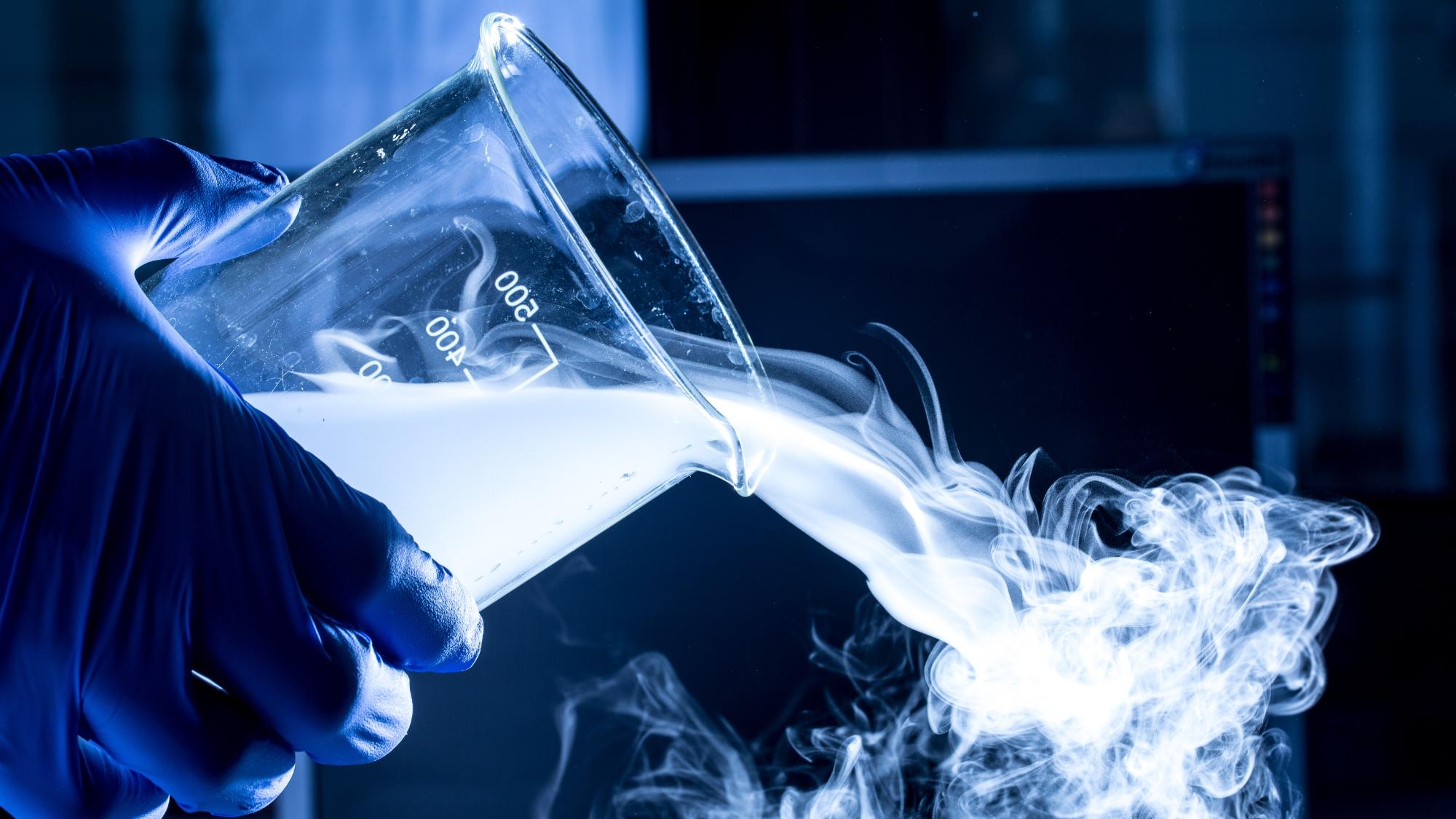
"ice cold - high speed."
Is it feasible or not? That is the question! Feasibility studies are very interesting and fun to do. We can think of new concepts for solving our clients issues and put them to the test. In this case, combining cryogenic temperatures with a high speed milling process and keeping it “simple” was a nice challenge.
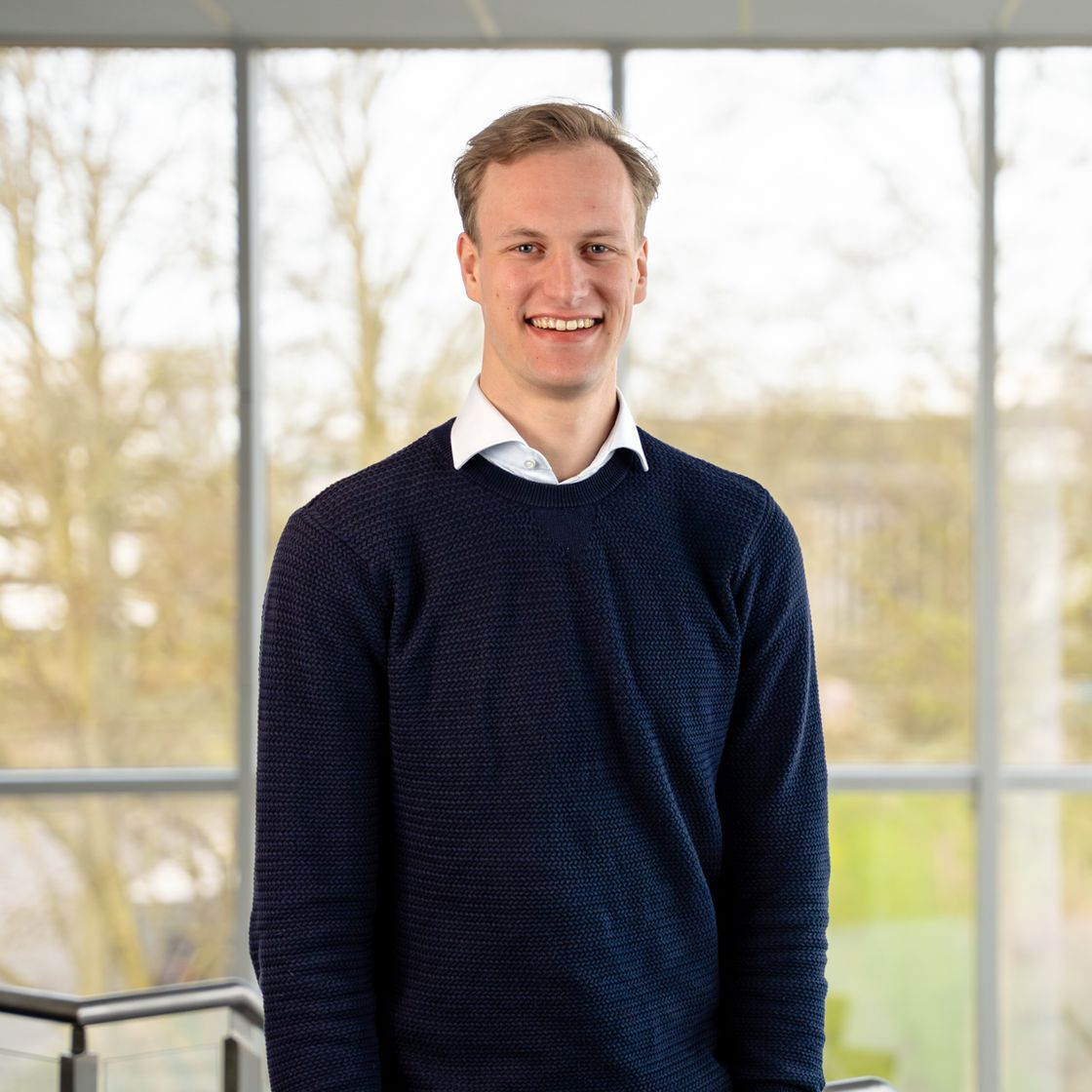