Cryogenics
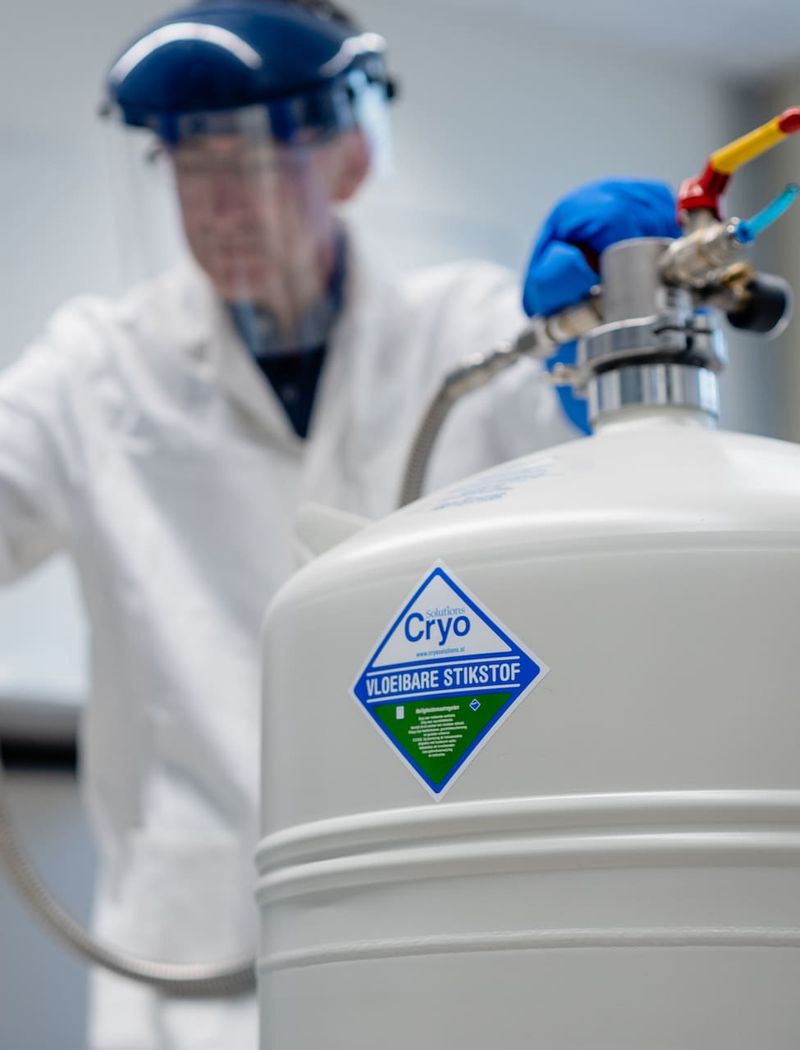
We provide contract R&D, typically starting from TRL 3 or 4. As a full-service design house, we offer a broad range of services tailored to our customers’ needs—ranging from start-ups to established OEMs, and from feasibility studies to product certification. We can support the full product creation process or specific phases, such as in a stage-gate approach. As part of the Demcon group, our services include: contract R&D, product development, feasibility studies, systems modeling, prototyping, pilot system testing, certification, clinical testing, manufacturing, and technical support starting from a low technology- readiness level.
Once the concept is validated, we enter the full product development phase where we transform ideas into practical, manufacturable products. This includes detailed industrial design, integration of manufacturing considerations, and thorough engineering analyses such as failure mode effects analysis (FMEA) and design-for-X (DfX). We collaborate closely with all stakeholders, including production partners, to optimize usability, safety, cost-efficiency, and assembly. Whether you’re a startup or an established OEM, we guide you through each step to ensure a smooth transition from prototype to market introduction.
Our support extends beyond production setup, including clinical testing and full clinical evaluation for medical products. We help scale your manufacturing with trusted partners and provide ongoing technical support throughout the product’s lifecycle. This includes maintenance, remote troubleshooting, and predictive service agreements, ensuring your product remains reliable and compliant throughout its market presence.
In this initial phase, we thoroughly explore new and emerging technologies to evaluate the feasibility of your concept. This involves detailed functionality analyses, identifying and ranking risks, and performing theoretical, analytical, or experimental proof-of-concept studies at various levels—from components and modules to entire systems. If necessary, we can go back to early research stages to investigate innovative breakthroughs, ensuring that your project starts on a solid technical foundation. Our approach combines creativity and rigorous evaluation to minimize uncertainties and avoid costly redesigns later in the process.
In this phase, we build pilot systems and beta prototypes using final production components and manufacturing methods. This allows us to finalize product design details and validate tooling, production processes, and testing protocols. We carry out pilot series production and null series for process validation and optimization. Alongside these activities, we support all necessary regulatory certifications and quality assurance testing to ensure compliance with industry standards such as CE, MDR, and IEC. Our expertise guarantees a reliable and robust production-ready product.you’re a startup or an established OEM, we guide you through each step to ensure a smooth transition from prototype to market introduction.