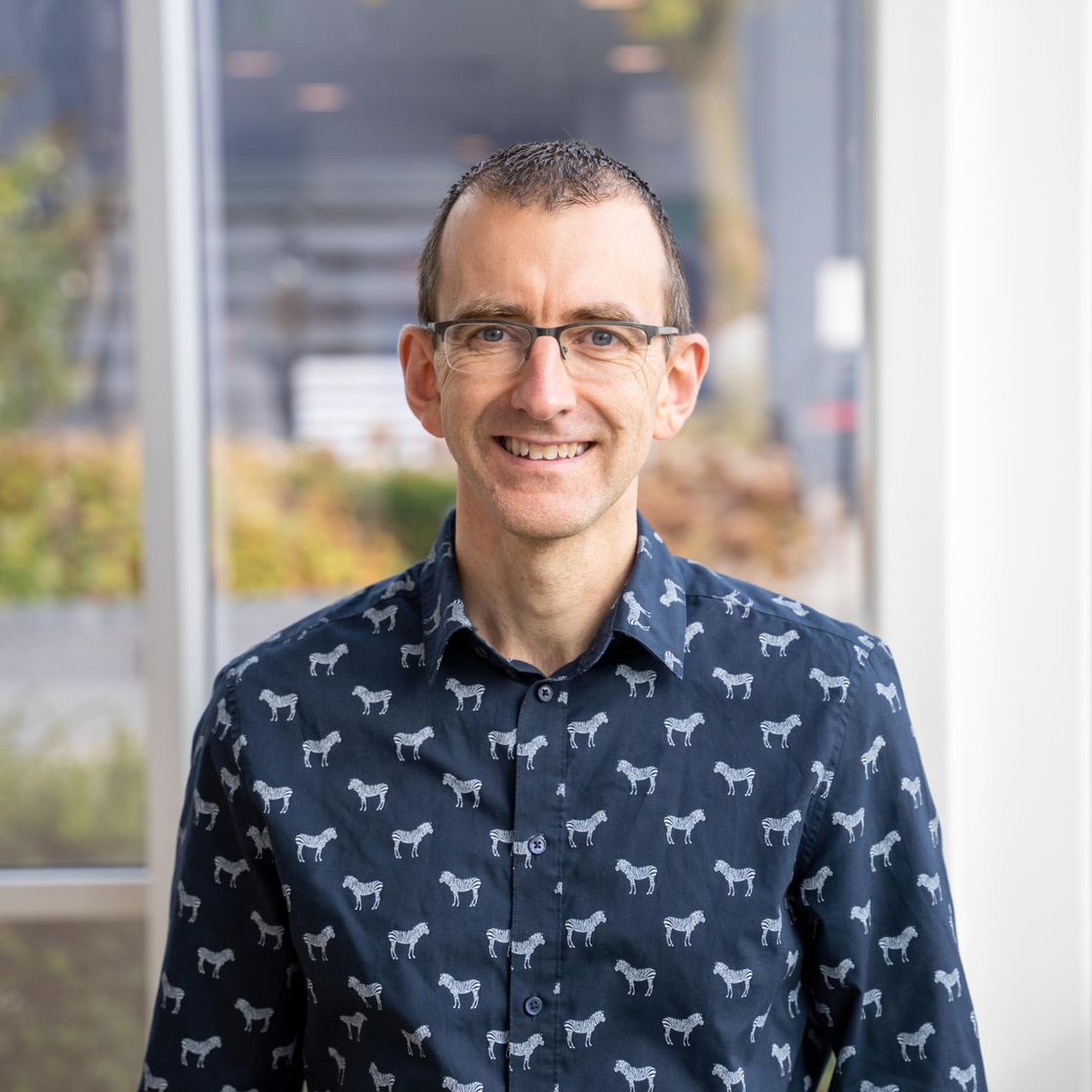
highlights
• low mass, low power consumption
• high cooling power
• compatible with various orbits and small satellite layouts
• flexible, scalable & modular
• heat switch function
• high reliability (no single-point-of-failure)
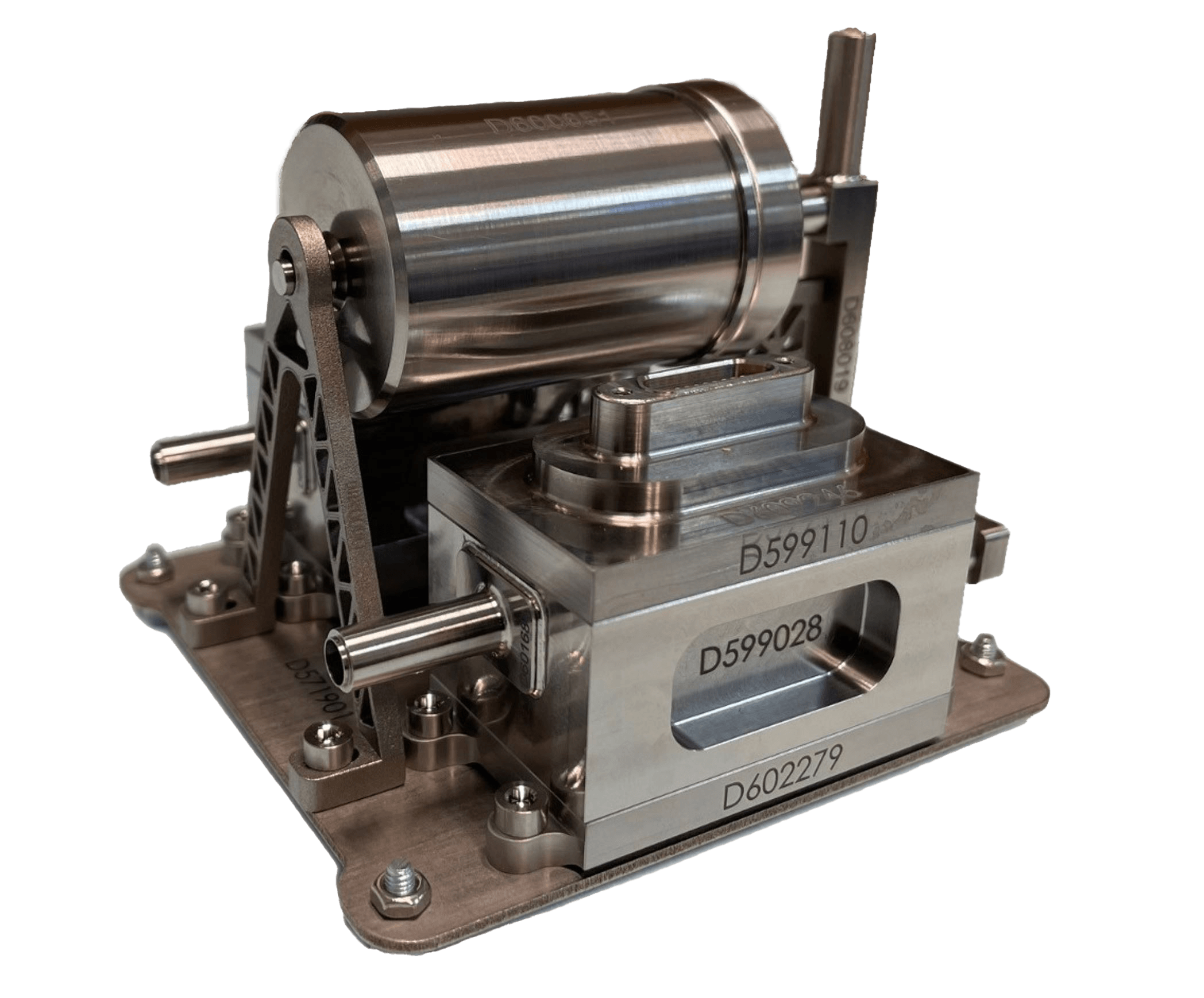
specifications.
-Cryocooler design, modelling and optimization
-Cold-stage successfully thermal tested
-194 mW @ 130 K
-Cool-down in 24 minutes
-Cold-stage successfully vibration tested
-Launch resistant
-Cold-stage successfully tested for zero-g performance (3-orientation testing). Can operate in all directions.
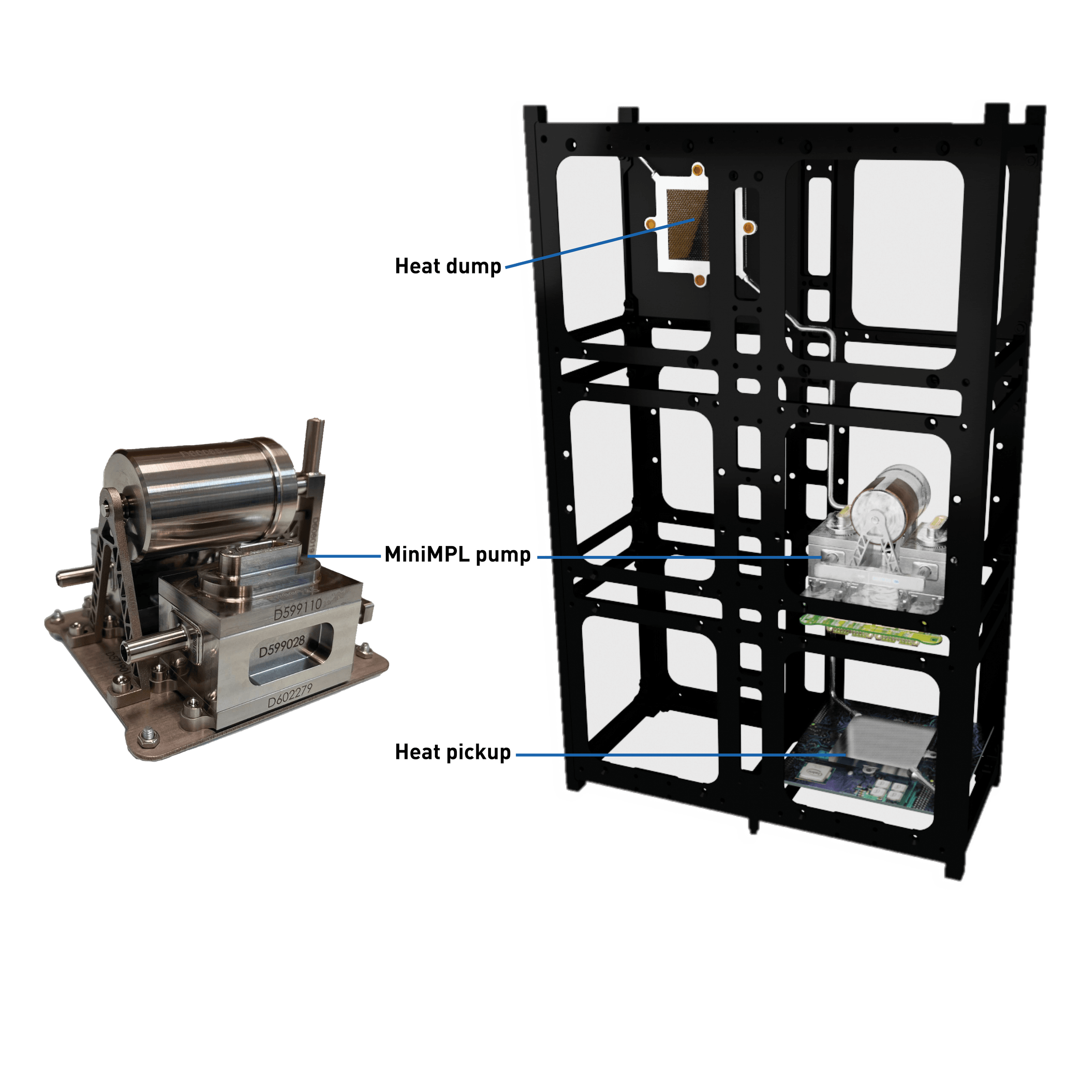
high-performance thermal control for CubeSats and microsatellites.
This compact thermal control system is specifically developed for small satellites such as CubeSats and microsatellites under 100 kg. Despite its minimal size—less than 1U in volume and approximately 1 kg in mass—it delivers exceptional performance, removing 40 to 100 watts of heat using only 2 to 5 watts of electrical input power. This allows satellite operators to manage high thermal loads without compromising limited onboard power budgets or system volume.
Thanks to its efficient design, the system is ideal for missions where thermal control is critical but available space and power are severely limited. It enables stable operating conditions even in the most compact platforms, supporting advanced payloads and extending mission lifetime.
enabling advanced space applications.
The system is designed to meet the thermal requirements of a wide range of satellite missions. It is particularly well suited for spacecraft equipped with high-heat components such as radar systems, active antennas, and electric propulsion units. Its active cooling capability also makes it highly effective for infrared detectors, which require precise and reliable temperature control for optimal performance.
An integrated heat switch function reduces the need for heater power during eclipse periods, further optimizing energy use and minimizing thermal stress. This feature is especially valuable for spacecraft operating beyond low Earth orbit or on interplanetary missions, where efficient power management is even more critical.
In addition, the system addresses thermal start-up challenges in loop heat pipe systems and supports flexible thermal routing in complex satellite designs—giving engineers greater freedom in payload and component placement.
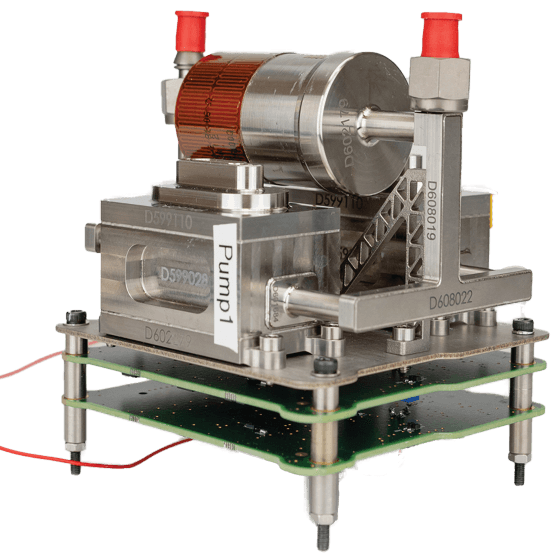
scalable, flexible, and designed for reliability.
Flexibility is a core strength of this thermal control solution. Its design includes highly flexible tubing that allows for mechanical decoupling between payloads and the satellite frame, preventing stress on sensitive electronics like printed circuit boards during launch vibrations or mechanical shocks. This not only protects critical hardware but also simplifies integration within a variety of platform architectures.
Scalability is built in, with the system capable of being extended to handle up to 200 watts of thermal dissipation. This makes it suitable for both small-scale CubeSats and larger, more demanding microsatellite missions. Redundancy of moving components ensures long-term operational reliability—an essential factor for missions that may last several years or venture far from Earth, where servicing is not an option.
With its compact design, high efficiency, mission versatility, and robust reliability, this thermal control system is a key enabling technology for the next generation of small satellite missions.
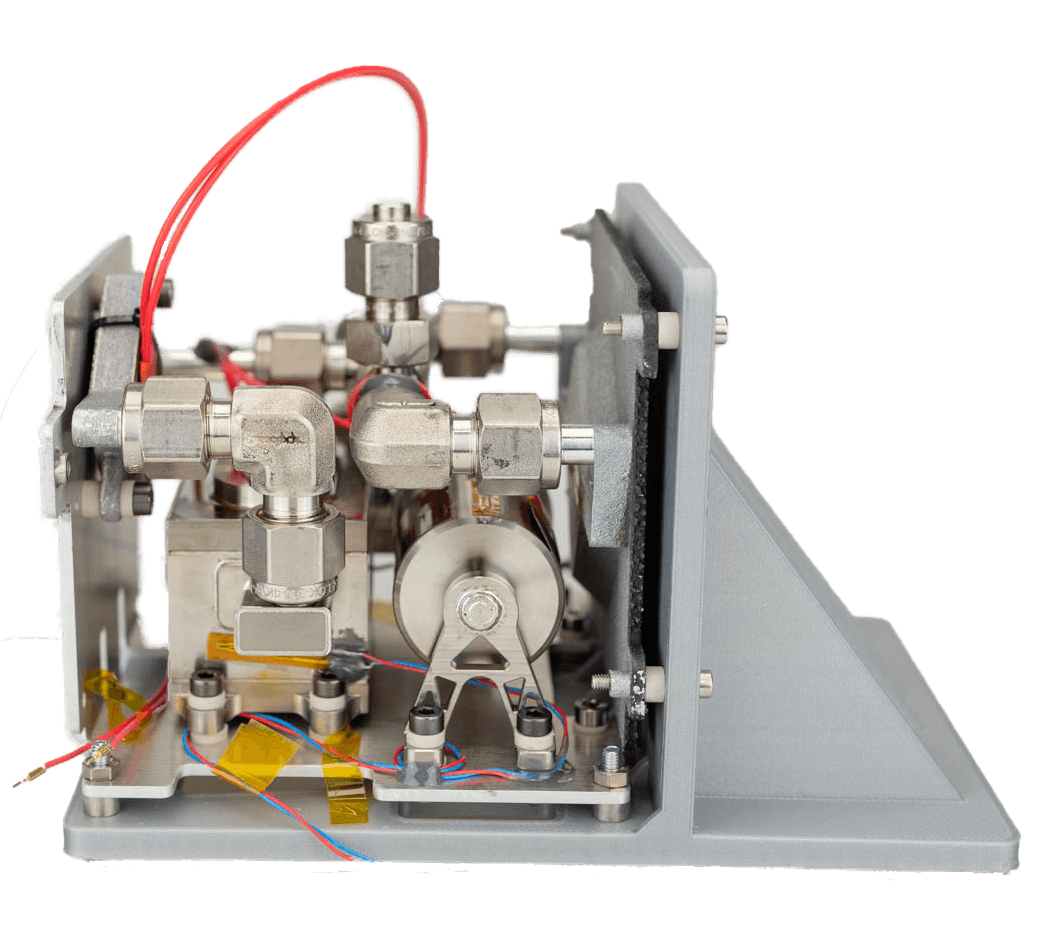
“our aim as OEM.”
It is our aim to bring this product (currently at TRL 5/6) to market within a consortium of specialized and capable partners and reach TRL 7/8 in 2024.
Demcon kryoz is industrializing the miniMPL with support of ESA and consortium partners.
Currently we are searching for lead users to partner with.
Interested? Please contact us!
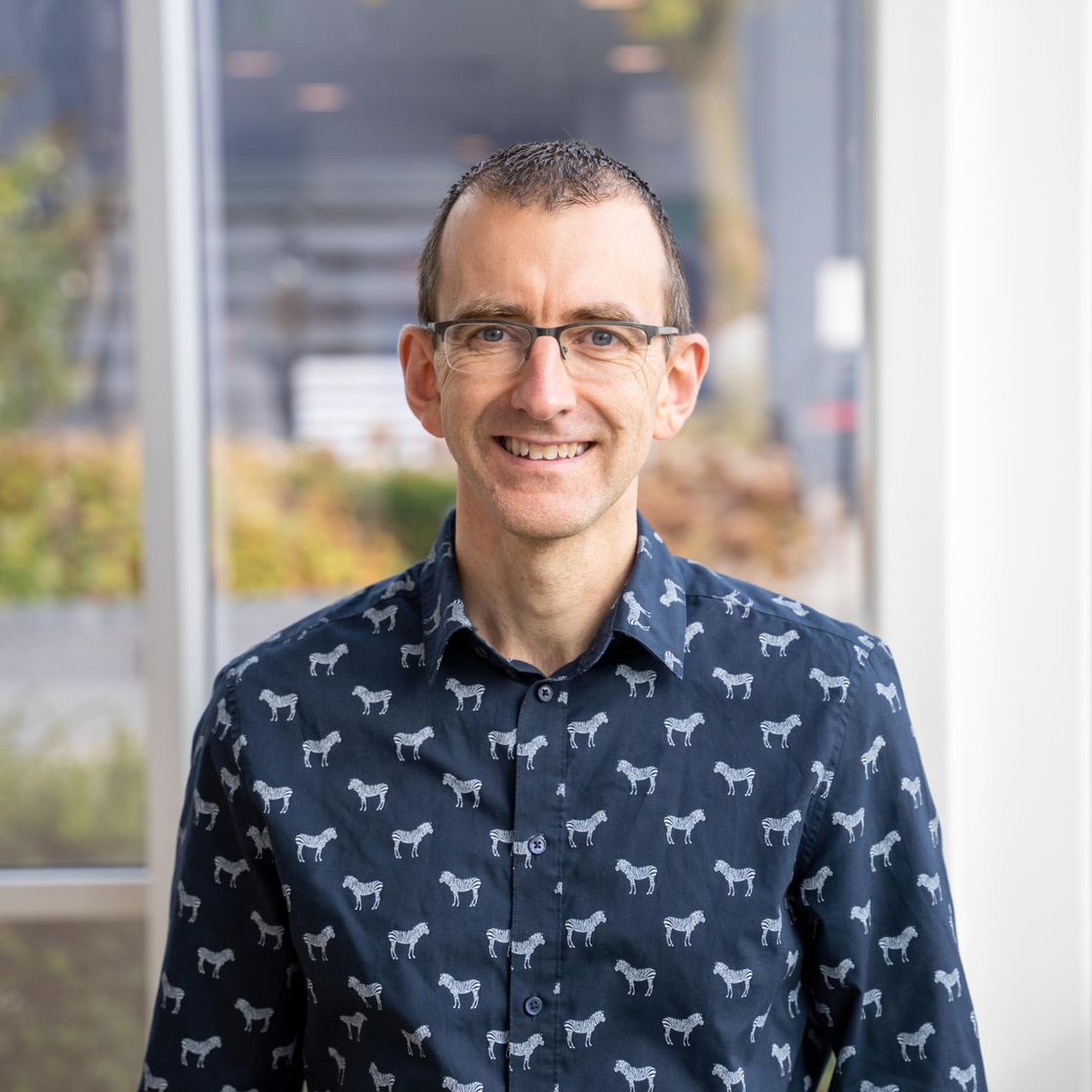